Dr.Al
Old Oak
This is one of three projects I'm going to be writing up in parallel (the other two are described here and here). They'll each be running at very different paces, with two at the design stage while one is being made, but I thought I'd start posting updates on them all at the same time. I don't have space to work on multiple projects at the same time, but that doesn't stop me thinking and planning!
This project is the furthest on of the three projects: I've got a design and I've got the wood so I just need to get on with making it.
The aim of this project is to make a simple shelf-unit for my other half. It'll be wall-mounted and look something like this:
Dimensions are subject to change (especially the board thickness) once I've finished preparing the planks.
The corner joints will be through dovetails as shown in the image. The plan is to use tapered dovetail housing joints for all the other joints. There will be a painted plywood back that will get screwed into a rebate in the back of the unit. Screwing the back on will allow it to be easily removed, which will allow it to be painted in different colours if desired.
It'll be made out of ash. The ash has been machined roughly to size and then left for a few months "in stick" on top of one of the bookshelves in the room in which it will eventually be fitted (I had to negotiate displacement of a rather large number of pairs of Dr Martens boots that normally live up there to make space for the wood to be stored).
Having taken the boards down from the top of the bookcase, I set them out on the workbench to see what I had to deal with:
There's quite a bit of bow in them (mainly across the width), so I think they'll need a fair amount of work with the planes to get them flat. I've started working on them this afternoon, mostly with the Axminster #5:
The grain of the first couple I've been working on has been quite variable in direction and I was getting a lot of tear-out. One was sorted with a bevel-up smoothing plane with a steep 50° bevel (and hence 62° cutting angle), the other one of the two I've planed so far was refusing to play ball even with that, so I resorted to the scraper plane, which did a lovely job (but gets a bit tiring after a while):
A couple of the boards had quite a bit of bark down one side. I decided to have a bit of fun and use a hatchet to hack it off:
I think that hatchet is designed for use for roofing and I'm sure this sort of thing would be easier with a single bevel hatchet, but it was quite fun anyway!
The weather's looking quite promising for tomorrow, which is nice as I think I'll have the garage door wide open as I've got a lot of planing to do.
This project is the furthest on of the three projects: I've got a design and I've got the wood so I just need to get on with making it.
The aim of this project is to make a simple shelf-unit for my other half. It'll be wall-mounted and look something like this:
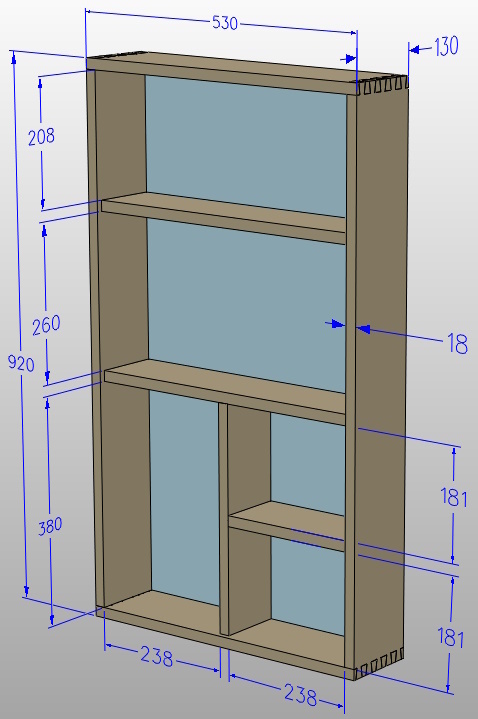
Dimensions are subject to change (especially the board thickness) once I've finished preparing the planks.
The corner joints will be through dovetails as shown in the image. The plan is to use tapered dovetail housing joints for all the other joints. There will be a painted plywood back that will get screwed into a rebate in the back of the unit. Screwing the back on will allow it to be easily removed, which will allow it to be painted in different colours if desired.
It'll be made out of ash. The ash has been machined roughly to size and then left for a few months "in stick" on top of one of the bookshelves in the room in which it will eventually be fitted (I had to negotiate displacement of a rather large number of pairs of Dr Martens boots that normally live up there to make space for the wood to be stored).
Having taken the boards down from the top of the bookcase, I set them out on the workbench to see what I had to deal with:
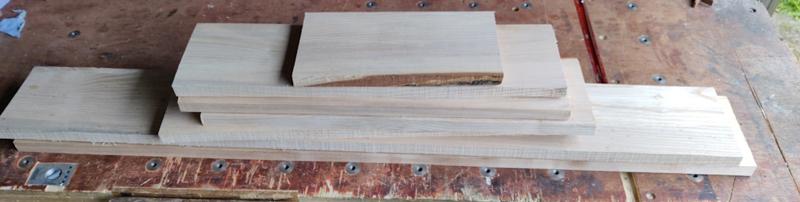
There's quite a bit of bow in them (mainly across the width), so I think they'll need a fair amount of work with the planes to get them flat. I've started working on them this afternoon, mostly with the Axminster #5:
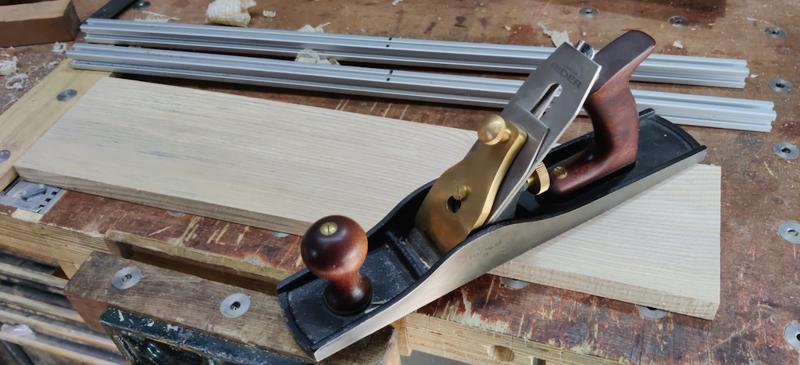
The grain of the first couple I've been working on has been quite variable in direction and I was getting a lot of tear-out. One was sorted with a bevel-up smoothing plane with a steep 50° bevel (and hence 62° cutting angle), the other one of the two I've planed so far was refusing to play ball even with that, so I resorted to the scraper plane, which did a lovely job (but gets a bit tiring after a while):
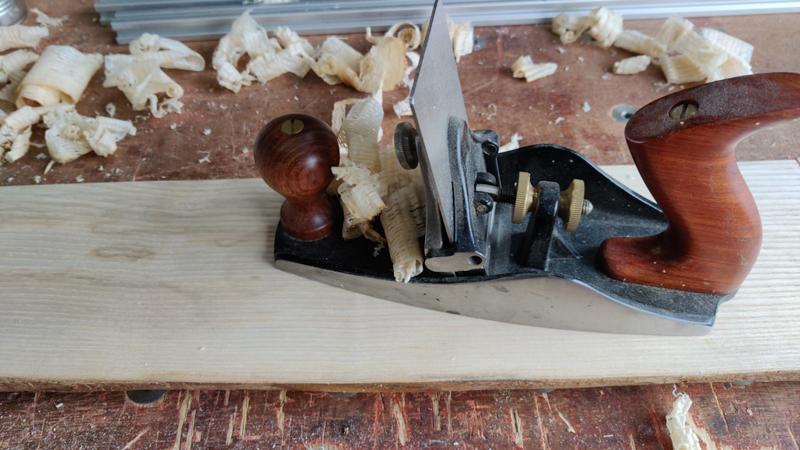
A couple of the boards had quite a bit of bark down one side. I decided to have a bit of fun and use a hatchet to hack it off:
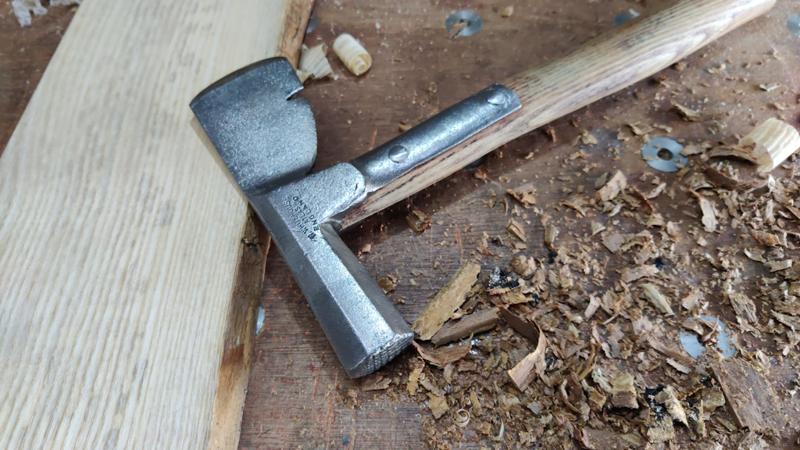
I think that hatchet is designed for use for roofing and I'm sure this sort of thing would be easier with a single bevel hatchet, but it was quite fun anyway!
The weather's looking quite promising for tomorrow, which is nice as I think I'll have the garage door wide open as I've got a lot of planing to do.
Last edited: